Products
KNOW ABOUT FOAM-IN-PLACE PACKAGING
Foam-in-place packaging involves creating a custom-fit foam cushion around a product on-demand. Two liquid chemicals are combined in a bag, and the mixture expands to surround the product, creating a protective mold. This process provides a snug, customized fit, offering superior protection during shipping and handling.
Steps of Foam-in-Place Packaging:
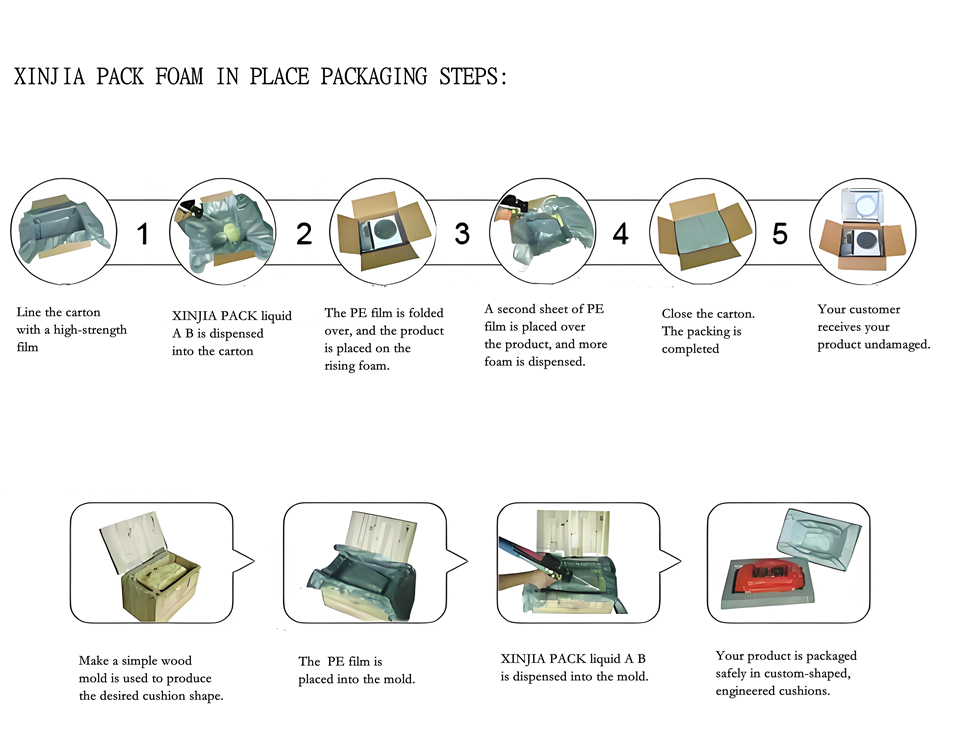
Foam-in-place packaging involves creating a custom-fit foam cushion around a product on-demand. Two liquid chemicals are combined in a bag, and the mixture expands to surround the product, creating a protective mold. This process provides a snug, customized fit, offering superior protection during shipping and handling.
Steps of Foam-in-Place Packaging:
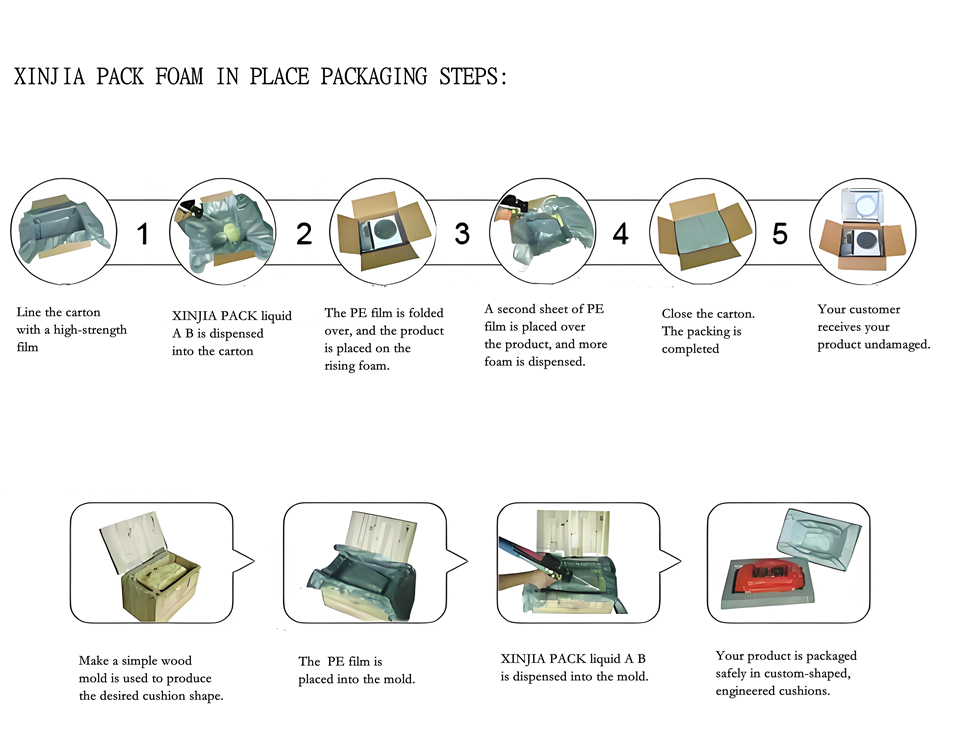
Total: 12
Page: 1 / 1
First
←Previous
Next→
End